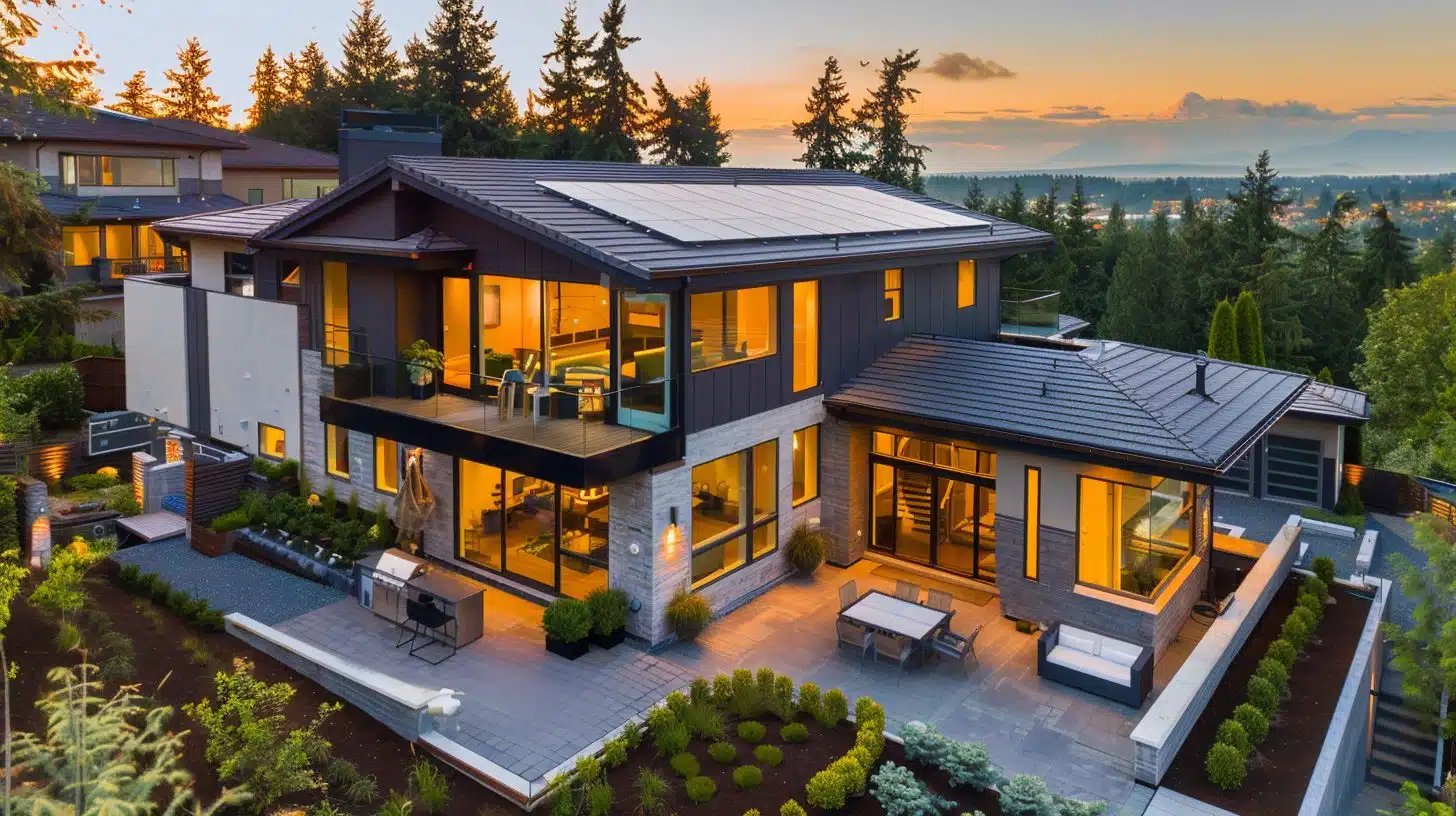
TESTING YIELDS
A BETTER HOME
Our detailed testing eliminates uncertainty during construction, providing clear insights that lead to a more efficient, comfortable, and energy-saving home by evaluating air leakage, ductwork, insulation, and more.
ESTABLISHING A HOME’S ENERGY PROFILE
A HERS Rating takes a comprehensive look at how a home uses energy, evaluating everything from insulation and air sealing to heating, cooling, hot water systems, windows, lighting, and even solar. Every component plays a role in overall efficiency, and the rating provides a clear benchmark to help homeowners, builders, and code officials make informed decisions. Whether the goal is meeting code requirements, lowering energy costs, or improving comfort, a HERS Rating offers a data-driven roadmap to better performance.
A key part of this evaluation is diagnostic testing, with a focus on three critical areas—envelope leakage, duct leakage, and mechanical ventilation. These tests remove the guesswork, quantifying air leakage, inefficiencies, and ventilation imbalances that can impact energy use, comfort, and indoor air quality.
ENVELOPE LEAKAGE
A blower door test is a crucial diagnostic tool used in a HERS Rating to measure a home's airtightness. By depressurizing or pressurizing the home with a calibrated fan, we can assess how much air is leaking through gaps, cracks, and other weak points in the building enclosure. To refine our analysis, we may also conduct zone pressure testing, which helps pinpoint specific rooms or areas that may be leakier than others and require special attention. Identifying and addressing these air leaks improves energy efficiency, enhances indoor comfort, and ensures compliance with Massachusetts energy codes.
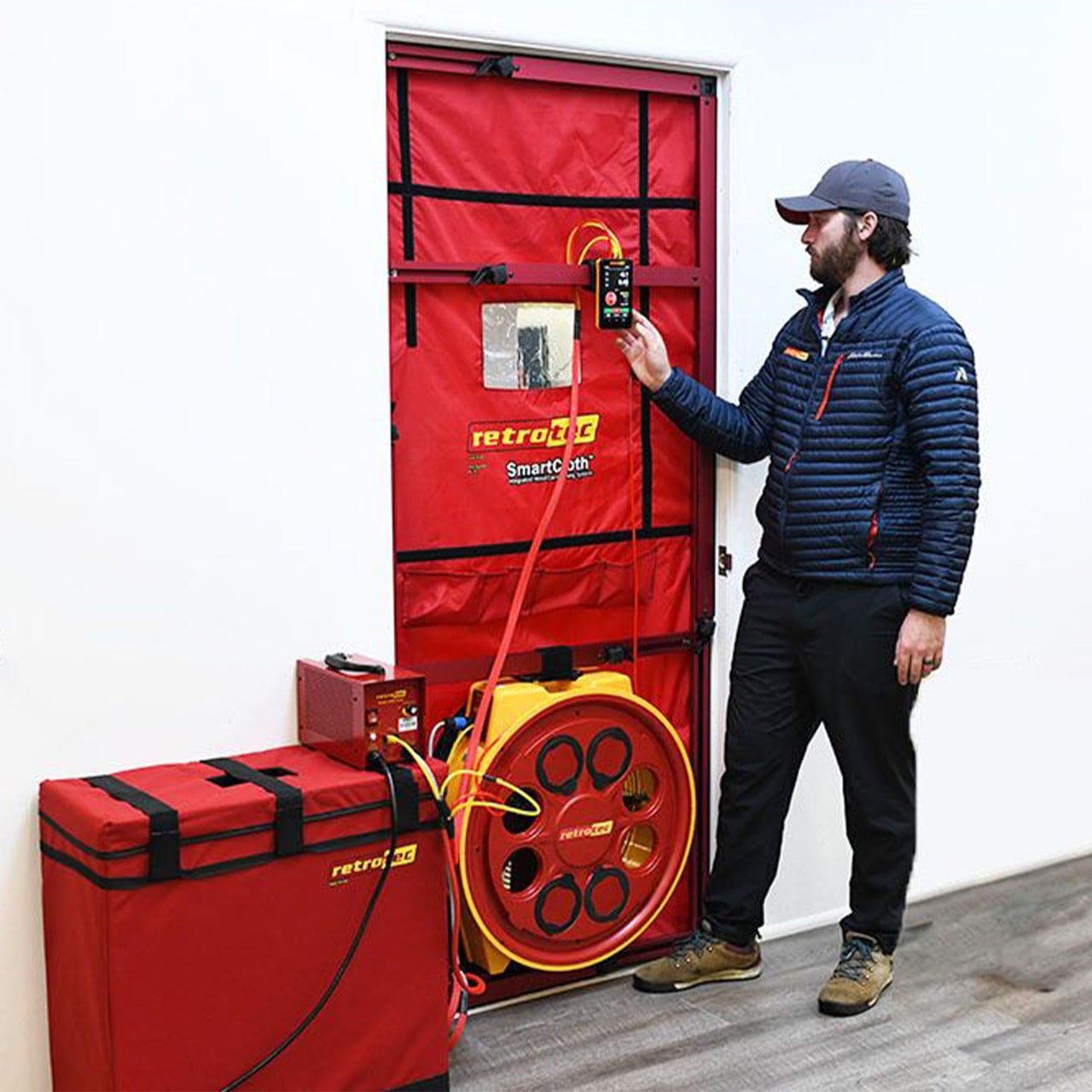
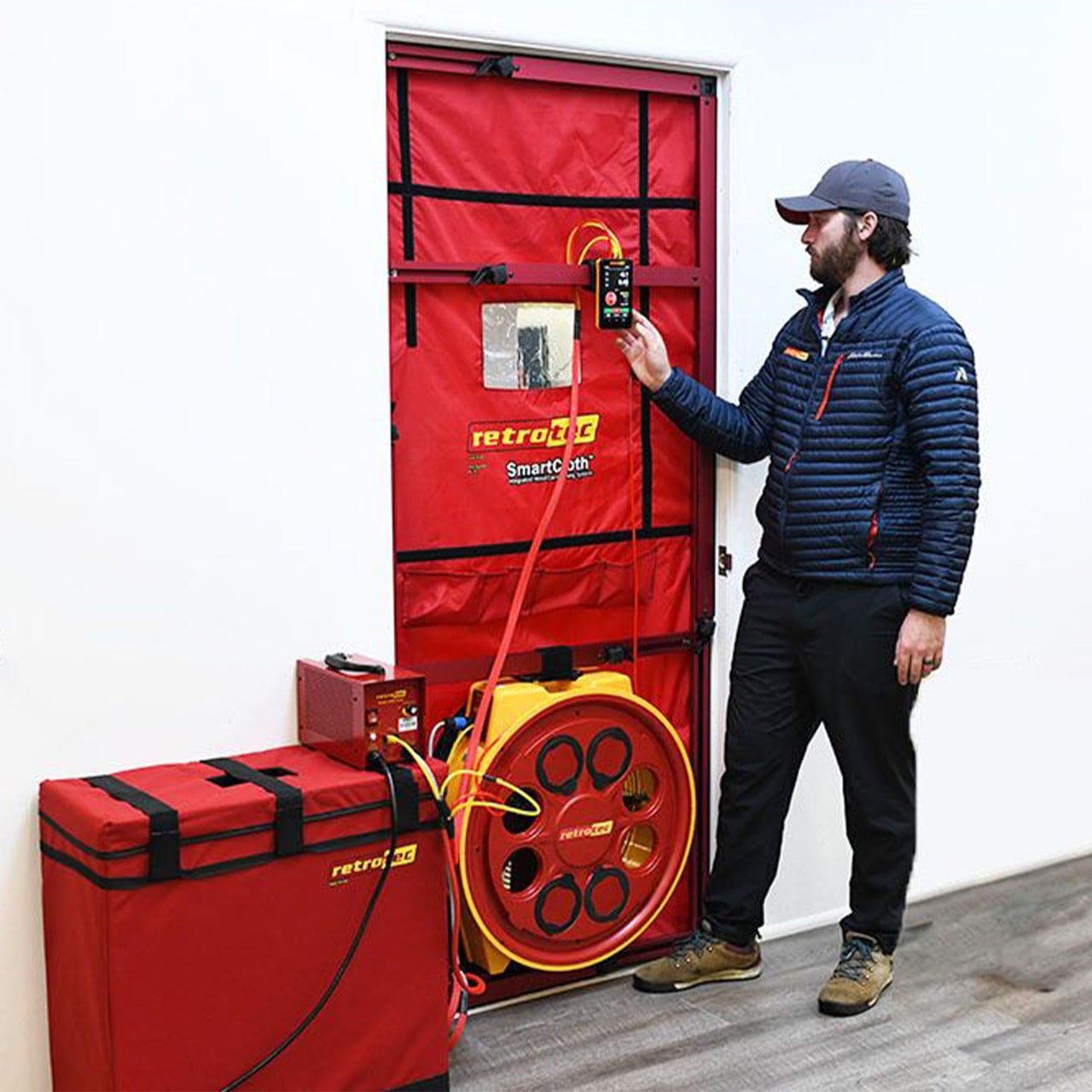
ENVELOPE LEAKAGE
A blower door test is a crucial diagnostic tool used in a HERS Rating to measure a home's airtightness. By depressurizing or pressurizing the home with a calibrated fan, we can assess how much air is leaking through gaps, cracks, and other weak points in the building enclosure. To refine our analysis, we may also conduct zone pressure testing, which helps pinpoint specific rooms or areas that may be leakier than others and require special attention. Identifying and addressing these air leaks improves energy efficiency, enhances indoor comfort, and ensures compliance with Massachusetts energy codes.
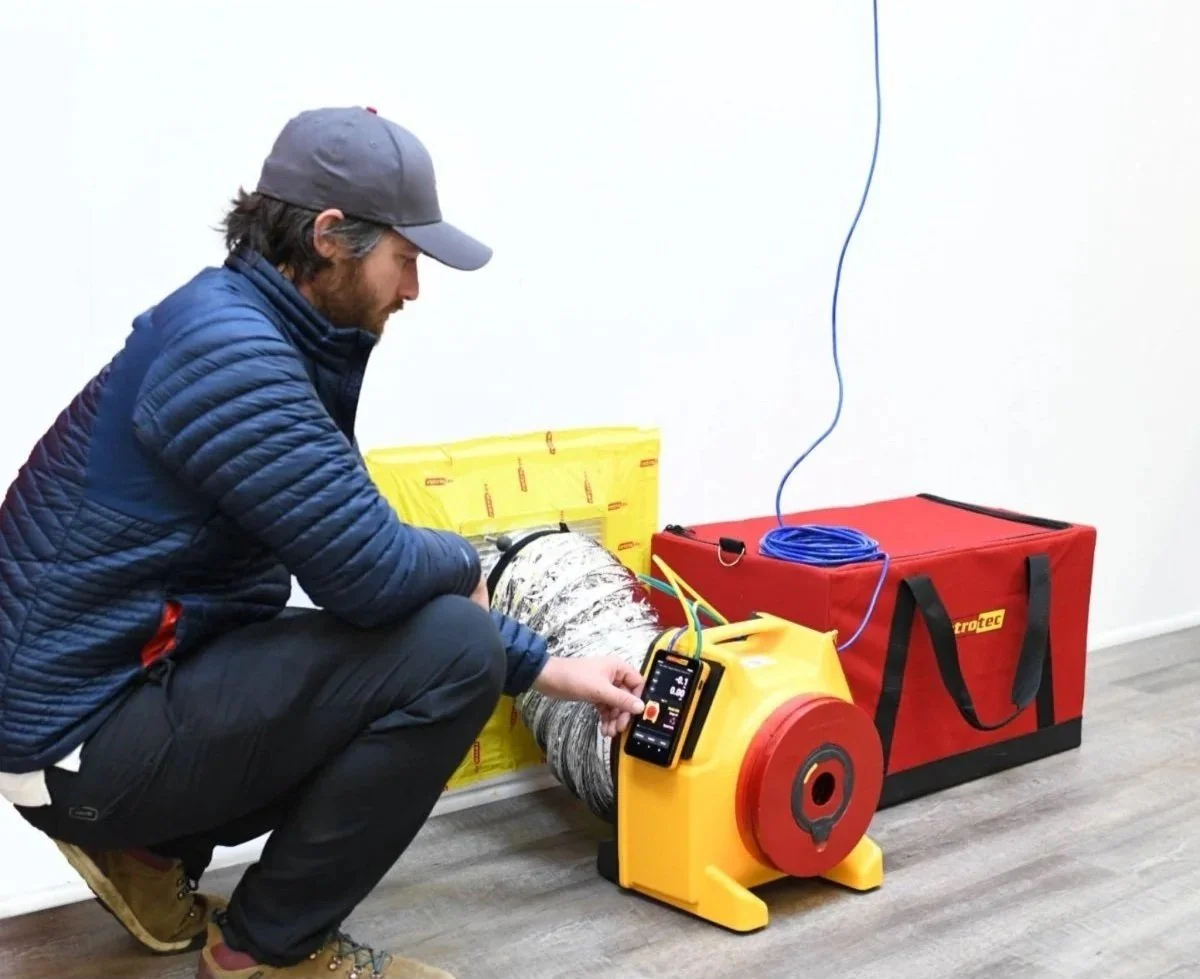
DUCTWORK LEAKAGE
Ductwork leakage testing measures how much air is leaking from a home’s heating and cooling ducts, ensuring the system operates efficiently. Using a calibrated fan and pressure gauge, we test the duct system to locate leaks that can waste energy, reduce comfort, and strain HVAC equipment. Excessive duct leakage forces systems to work harder, leading to higher energy bills and uneven heating or cooling. By minimizing leakage, homeowners can improve indoor air quality, maximize system performance, and meet HERS Rating requirements for energy code compliance.
MECHANICAL VENTILATION
Mechanical ventilation testing ensures that whole-home balanced ventilation systems deliver the correct amount of fresh air while efficiently exhausting stale air. Using specialized flow measurement tools, we verify that supply and exhaust rates align with design specifications, ensuring proper air exchange without energy waste. Balanced ventilation is crucial for maintaining healthy indoor air quality, controlling moisture, and preventing pressure imbalances that can lead to drafts or inefficiencies. Accurate testing helps homeowners and builders achieve energy code compliance, optimize comfort, and improve overall system performance.
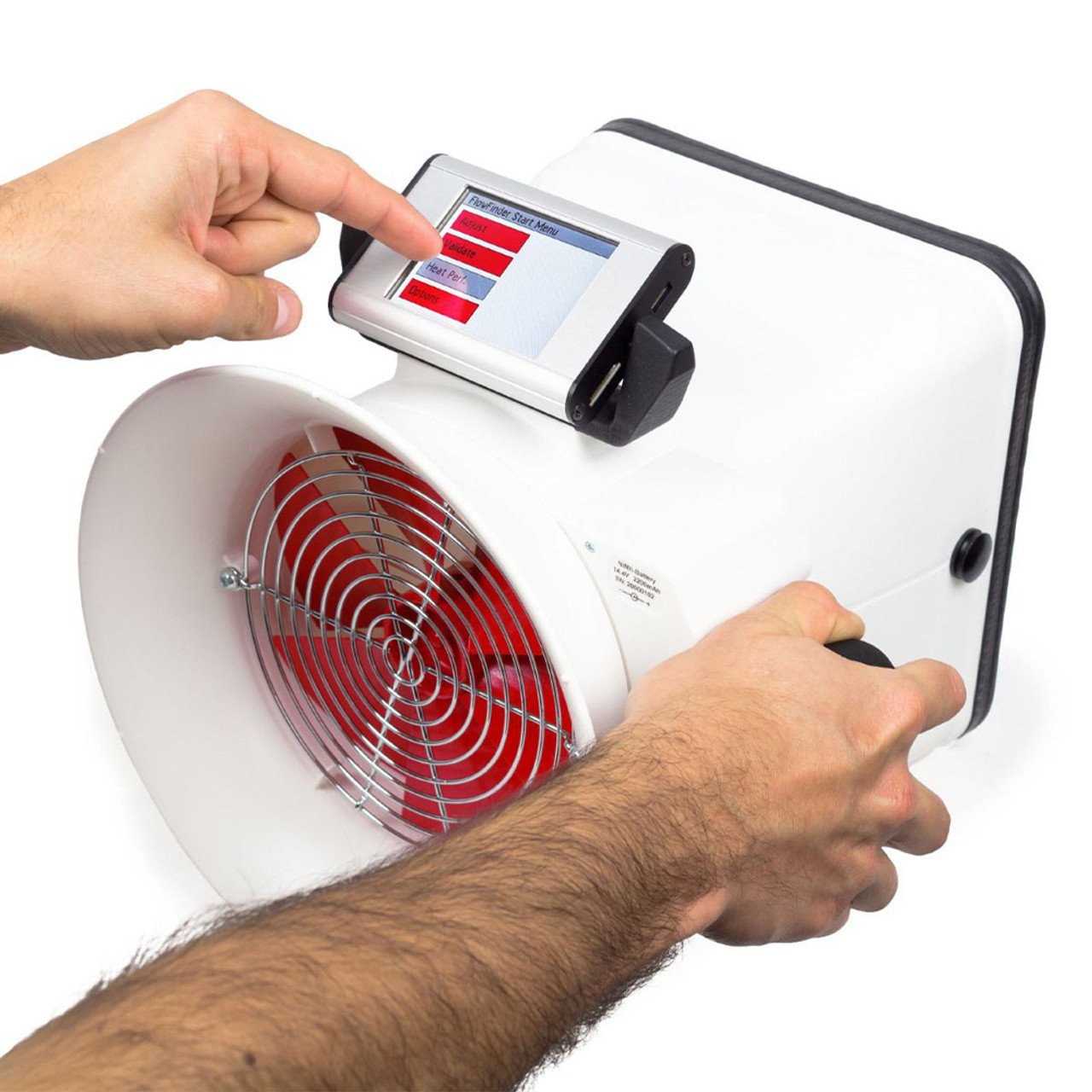
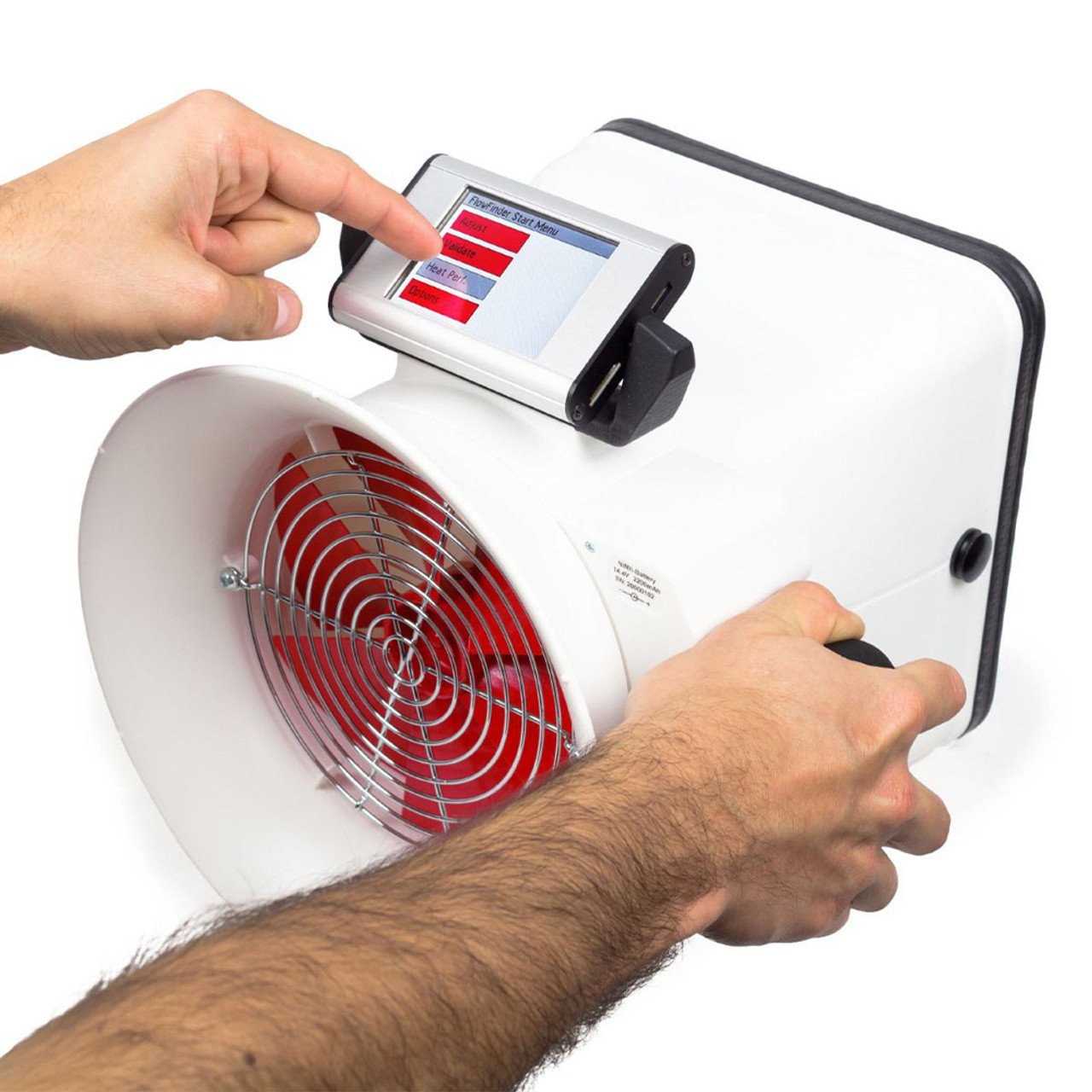
MECHANICAL VENTILATION
Mechanical ventilation testing ensures that whole-home balanced ventilation systems deliver the correct amount of fresh air while efficiently exhausting stale air. Using specialized flow measurement tools, we verify that supply and exhaust rates align with design specifications, ensuring proper air exchange without energy waste. Balanced ventilation is crucial for maintaining healthy indoor air quality, controlling moisture, and preventing pressure imbalances that can lead to drafts or inefficiencies. Accurate testing helps homeowners and builders achieve energy code compliance, optimize comfort, and improve overall system performance.
ROUNDING OUT
ENERGY EFFICIENCY
Building an energy-efficient home involves thoughtful attention to a variety of factors, including insulation, windows, lighting, appliances, and more. Each component impacts the home’s overall performance and energy use. We assess and quantify the elements below to ensure that your home is as efficient as possible, optimizing energy use and comfort throughout.
Insulation R-Values – Higher R-values improve resistance to heat transfer, enhancing efficiency and comfort by reducing heating and cooling loads.
Window & Door U-Factor and SHGC – Lower U-factors and optimized SHGC values help minimize heat loss in winter and limit heat gain in summer, improving energy performance.
Lighting – Energy-efficient lighting lowers overall electrical demand while improving illumination quality and longevity.
Appliances (Stove, Fridge, Washer, Dryer, Dishwasher) – High-efficiency models reduce energy, water consumption, and internal heat gain, while maintaining performance.
Location of HVAC, Hot Water Equipment & Ductwork – Placing equipment and ductwork within conditioned spaces reduces energy loss and improves system efficiency.
Solar – On-site solar generation can offset grid electricity use, lowering operational costs and increasing energy independence.
Water Distribution Lengths – Shorter runs reduce heat loss and improve hot water delivery efficiency, cutting down on energy and water waste.
Volume of the Home – A well-designed building envelope optimizes conditioned space, minimizing unnecessary energy demand for heating and cooling.