
YEAR ROUND COMFORT
Maximize insulation and air sealing to create an efficient, comfortable, and healthy home.
Sea level rise is caused primarily by two factors related to global warming: the added water from melting ice sheets and glaciers, and the expansion of seawater as it warms. Since 1993, global sea levels have risen 4”. - NASA
SOLUTIONS FOR NEW HOMES
Today’s homes are generally more complex when compared to existing New England homes built in past decades and centuries. With a closer focus on creating a more energy efficient housing market, spray foam is primarily used to help achieve energy rating goals. With heating and cooling equipment located in attics and basements, more often than not, these areas are now falling into conditioned spaces. Spray foam is an outstanding choice for these applications.
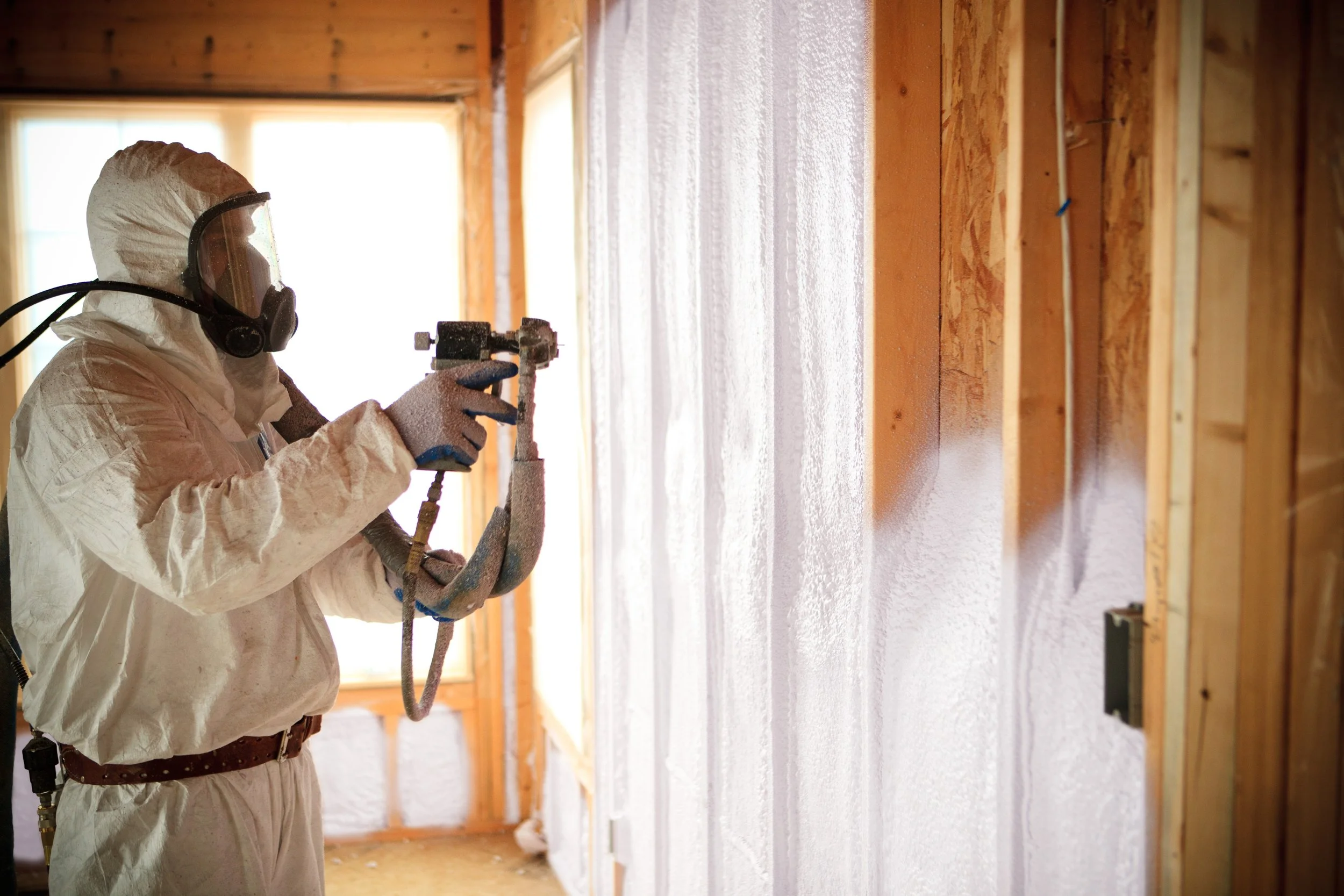
-
The best way to think of a conditioned space is to envision an area in a home that is directly heated or cooled with equipment, such as a living or bedroom. Insulation for these locations are required. Here’s where it gets a little complicated. Many of the houses designed today with a conventional basement and attic will see heating and cooling equipment located in both the basement AND attic. When this is the case, energy modeling software and building science best practices recommend insulating at the perimeter of these spaces. Why? Insulting at the perimeter of these areas help equipment operate more efficiently by improved thermal regulation of the spaces year round. Also, any leakage from ductwork or heat/cooling created from mechanical equipment stays within the thermal envelope rather than escaping to the outdoors.
-
Open Cell
Open cell foam or half pound foam
R3.7-R4.1
Air barrier
Can be applied to wood substrates and over closed cell foam.
Generally applied to exterior wood frame walls. Can be applied under a rubber roof or over closed cell foam.Closed Cell
Closed cell foam or two pound foam. Must be a low Global Warming Potential (GWP) product in Massachusetts.
R6.8-R7.5
Air barrier
Moisture barrier
Adds structure to a building assemblyGenerally applied to exterior wood frame walls, roofs, basement and crawl space walls, and exposed floors.
Can be applied to wood, concrete, field stone, granite, metal, and more.
-
An intumescent coating is a special paint designed to be applied to exposed spray foam in areas that are deemed accessible to storage or have mechanical equipment. Providing a 15 minute fire rating, an intumescent coating helps passively increase a building’s resistance to fire. When exposed to extreme temperatures, these coatings expand. The coatings lose density as they expand; as a result, they act as an insulator.
An intumescent coating consists of many chemicals, all suspended in a binder. The binder softens in response to heat exposure, letting the suspended chemicals react. These chemicals produce a foam, which hardens into an insulating material called “char.”
Intumescent coatings are often overlooked; however, they play an integral role in creating a safe environment.

SOLUTIONS FOR EXISTING HOMES
As the infographic to the left depicts, outdoor air enters a home (infiltration) through the building envelope, mainly the sill of a basement, penetrations through basement walls (oil, electrical, and gas service lines, etc.), at the band joist (area between floors) and leaky windows and doors. Depending on the time of year, the air entering your home can carry moisture, dust, and allergens. Exfiltration on the other hand, is when indoor conditioned air escapes outside, mainly through penetrations in your ceiling to your attic. Either way, when one or both areas are not air sealed correctly, indoor air quality problems, condensation, excess energy use, and comfort complaints may arise.
-
After a house is properly air sealed and has a deep layer of insulation, it is imperative to mitigate and control sources of moisture as well as calculate ventilation for unconditioned attics. In many retrofit applications, typically older homes, it is common to find dirt crawl spaces, which are a major moisture concern. Sealing this area with a vapor barrier keeps moisture at bay and greatly reduces the risk of a variety of problems that may arise. Venting bath and kitchen fans help expel combustion gases, moisture and odors. Adding attic ventilation if necessary helps cold weather homes like we have in the northeast to maintain a cold roof temperature to avoid ice dams created by melting snow and to expel any moisture that moves from the conditioned living space to the attic.
-
Air sealing is a cost-effective way to cut heating and cooling costs, improve durability, increase comfort, and create a healthier indoor environment.
-
Once the building envelope of a home has been properly air sealed, adding insulation is the next step in improving efficiency and comfortability. Measured in R-Value, a quantitative measure of an assembly or material resistance to heat flow for a unit temperature difference and a unit area, insulation slows the transfer of heat through conduction, convection and radiation thus keeping your house warmer in the winter and cooler in the summer.
REBATES AND INCENTIVES
Having spent nearly 10 years working within the Mass Save program, we have intimate knowledge of the program and can help our clients identify qualifying rebates and incentives to help reduce expenses, while still achieving their energy efficiency goals. Did you know Mass Save offers up to 75% to 100% off qualifying insulation upgrades, no cost air sealing, as well as generous rebates on heating, cooling, and water heating equipment? These upgrades may even qualify for the 0% Heat Loan.
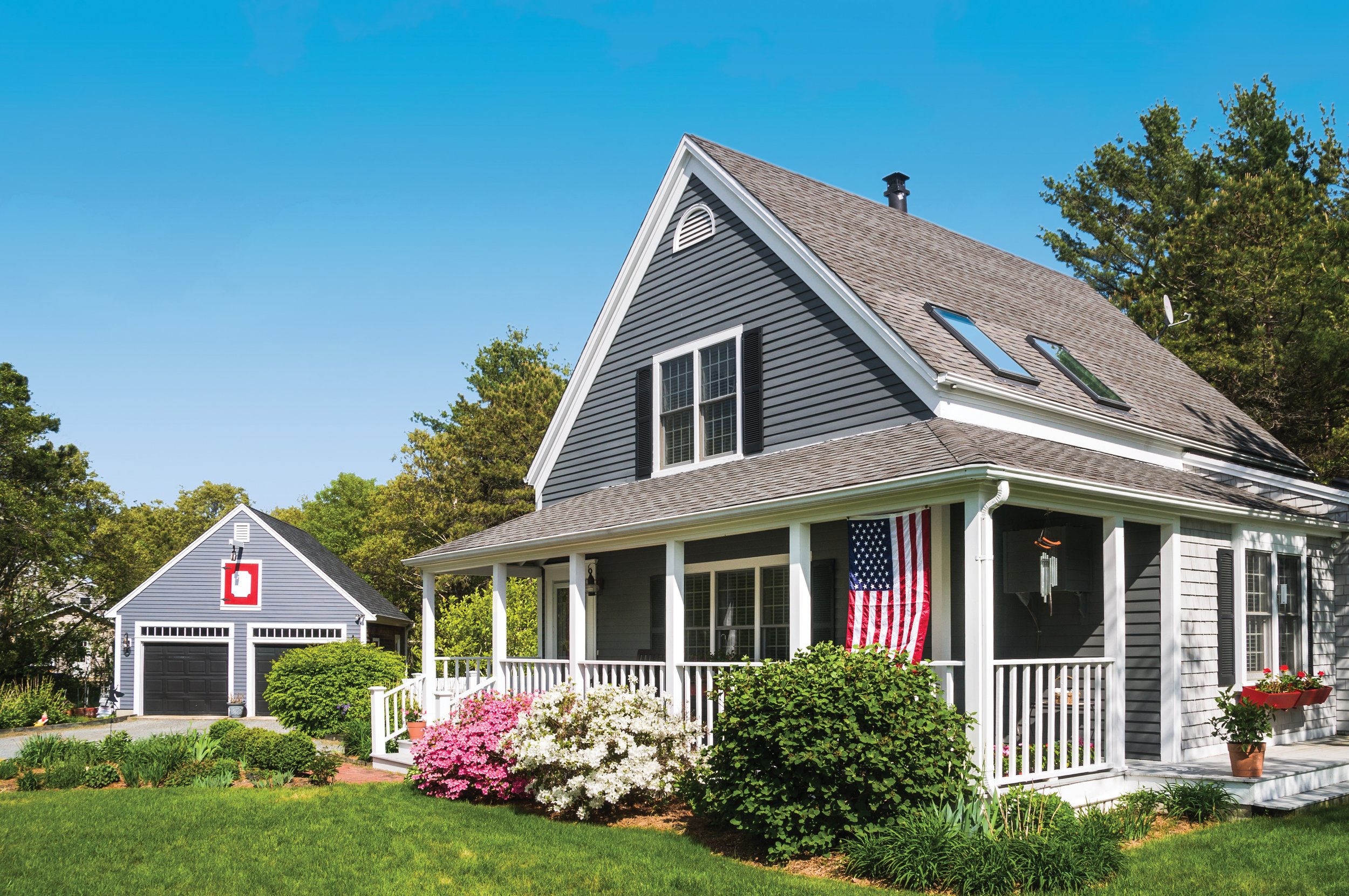
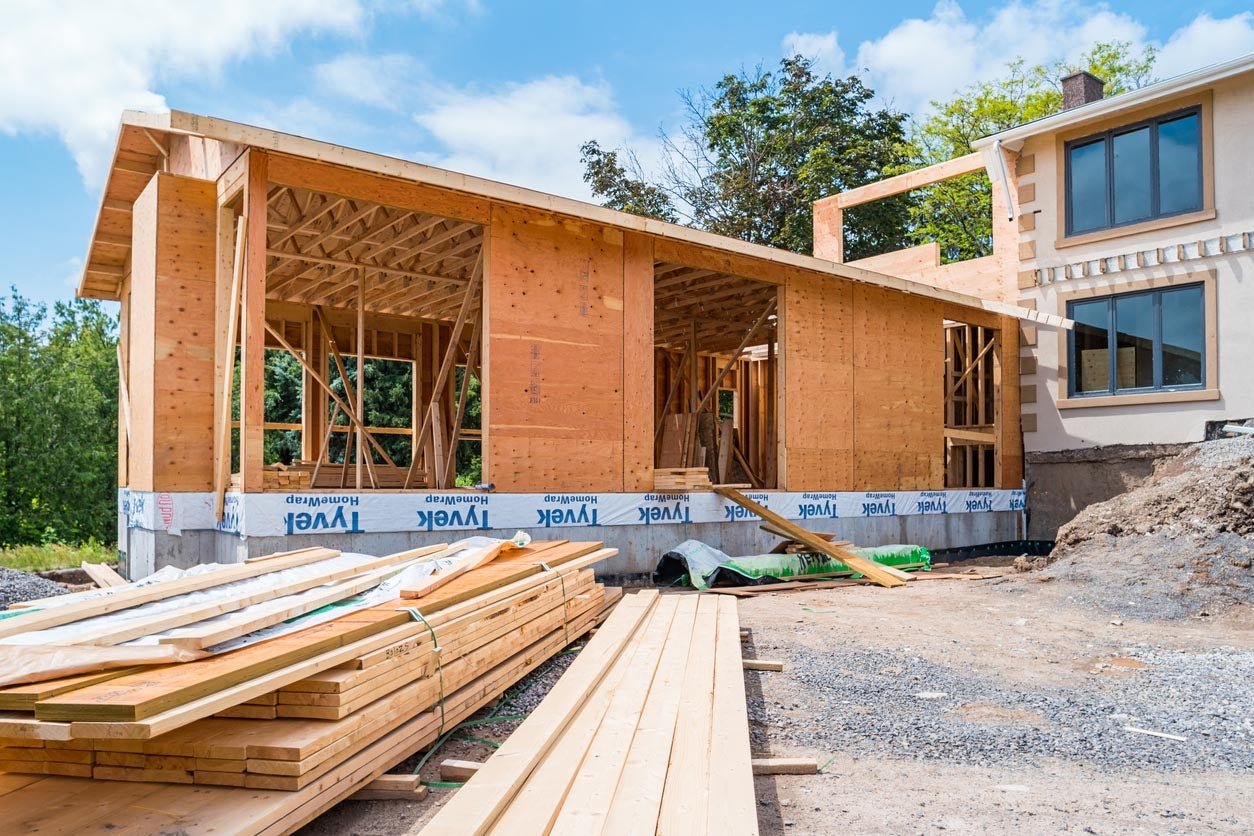
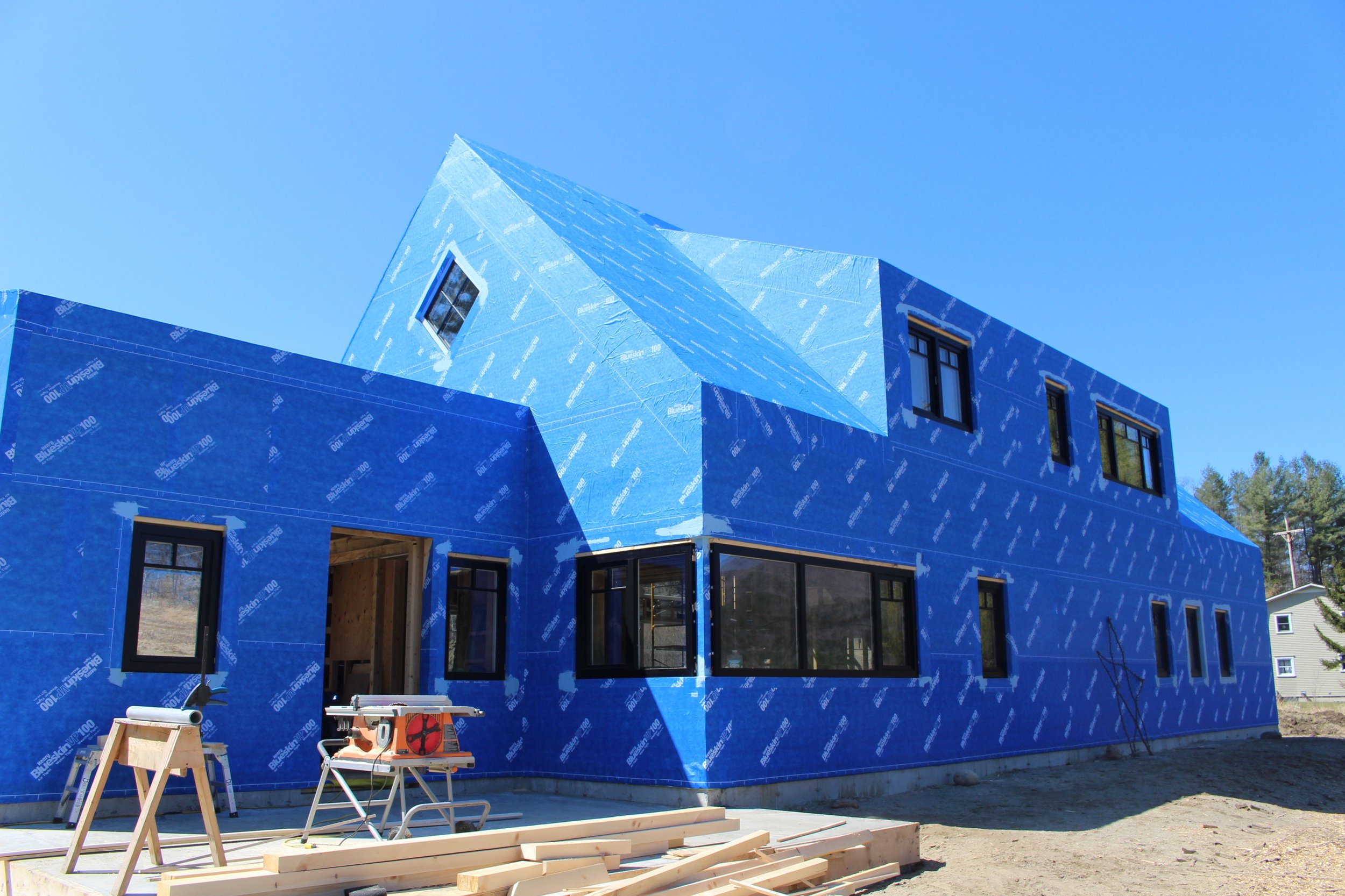
OUR PREFERRED
INSULATION PRODUCTS
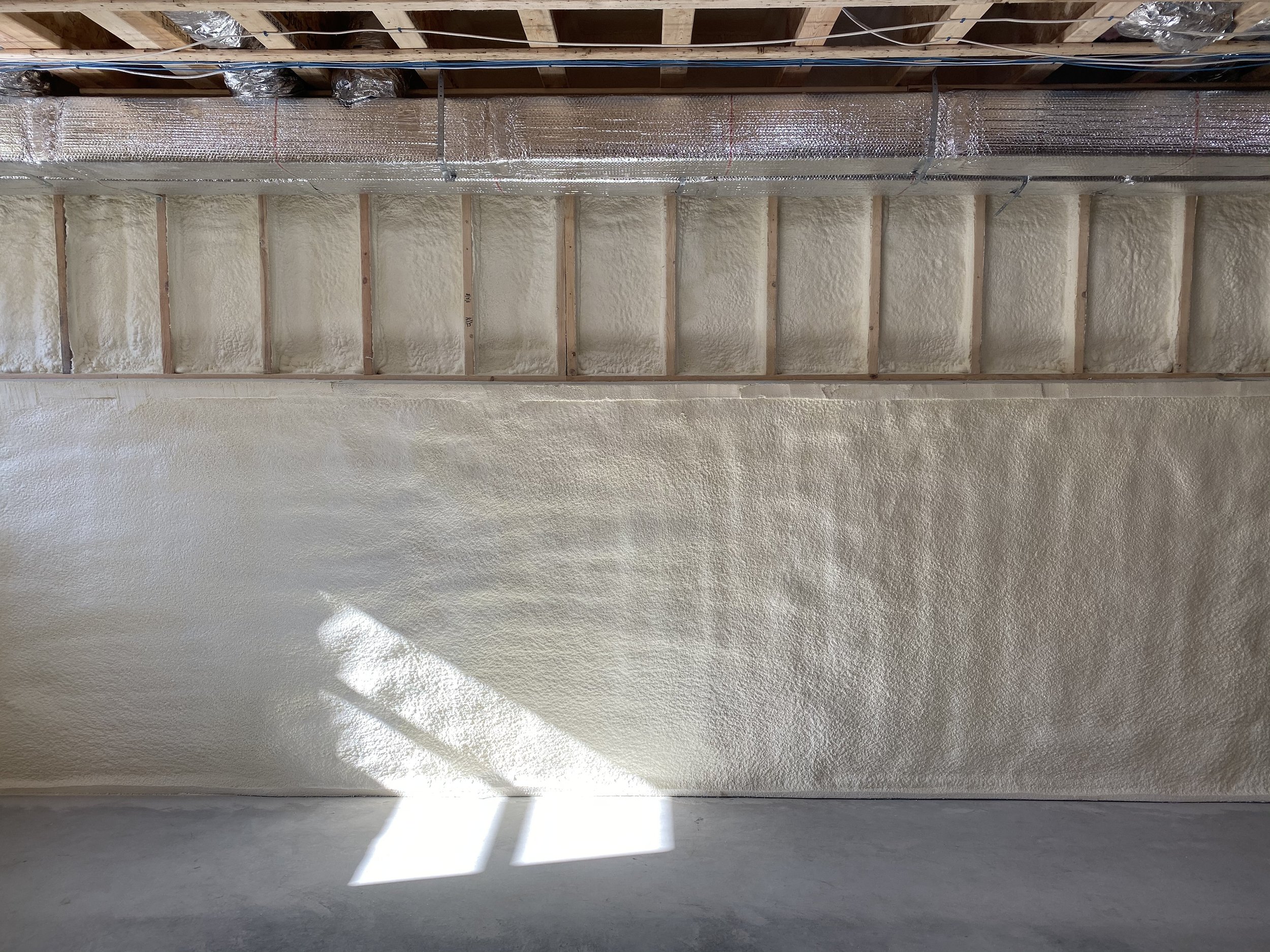
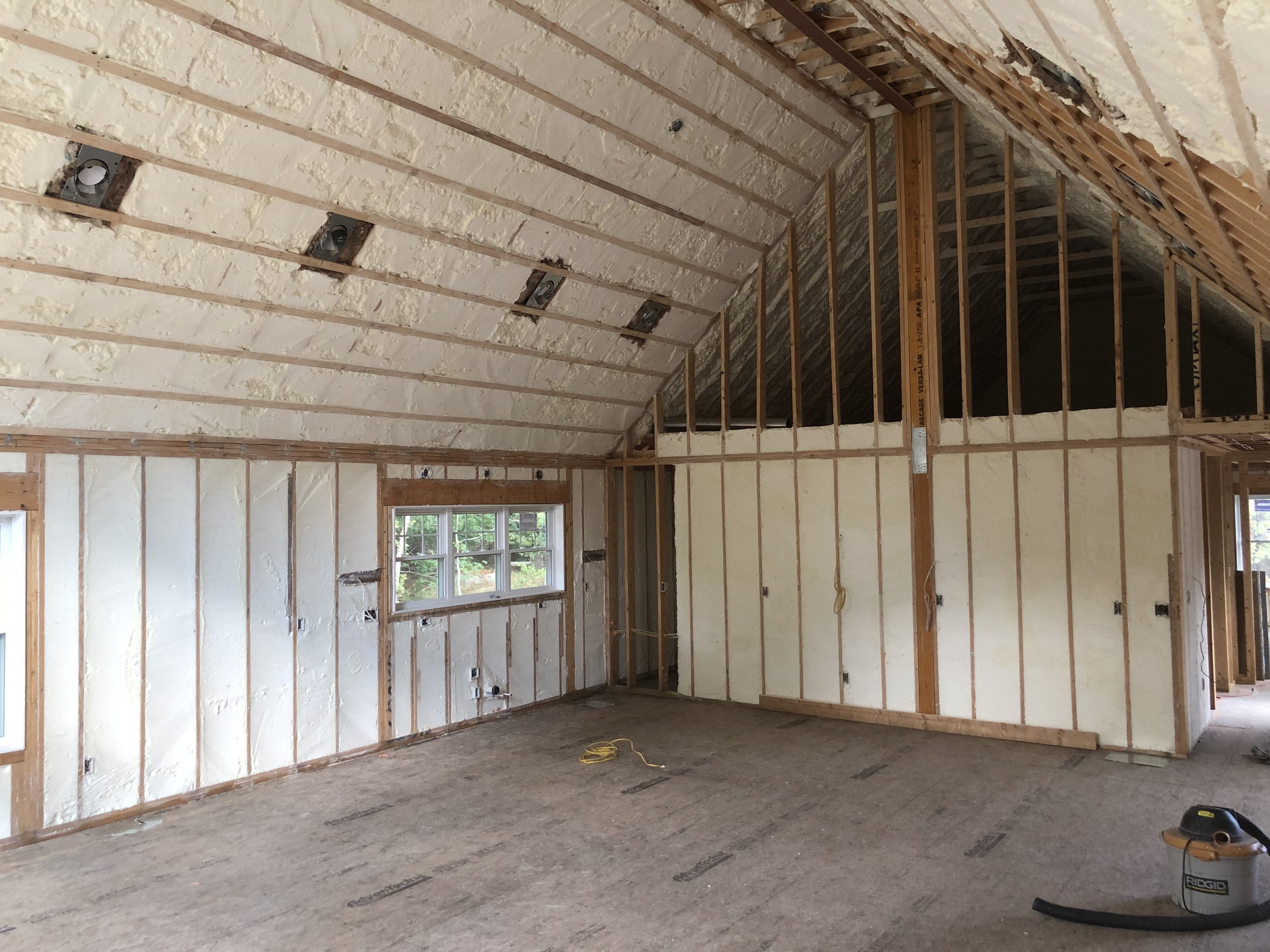

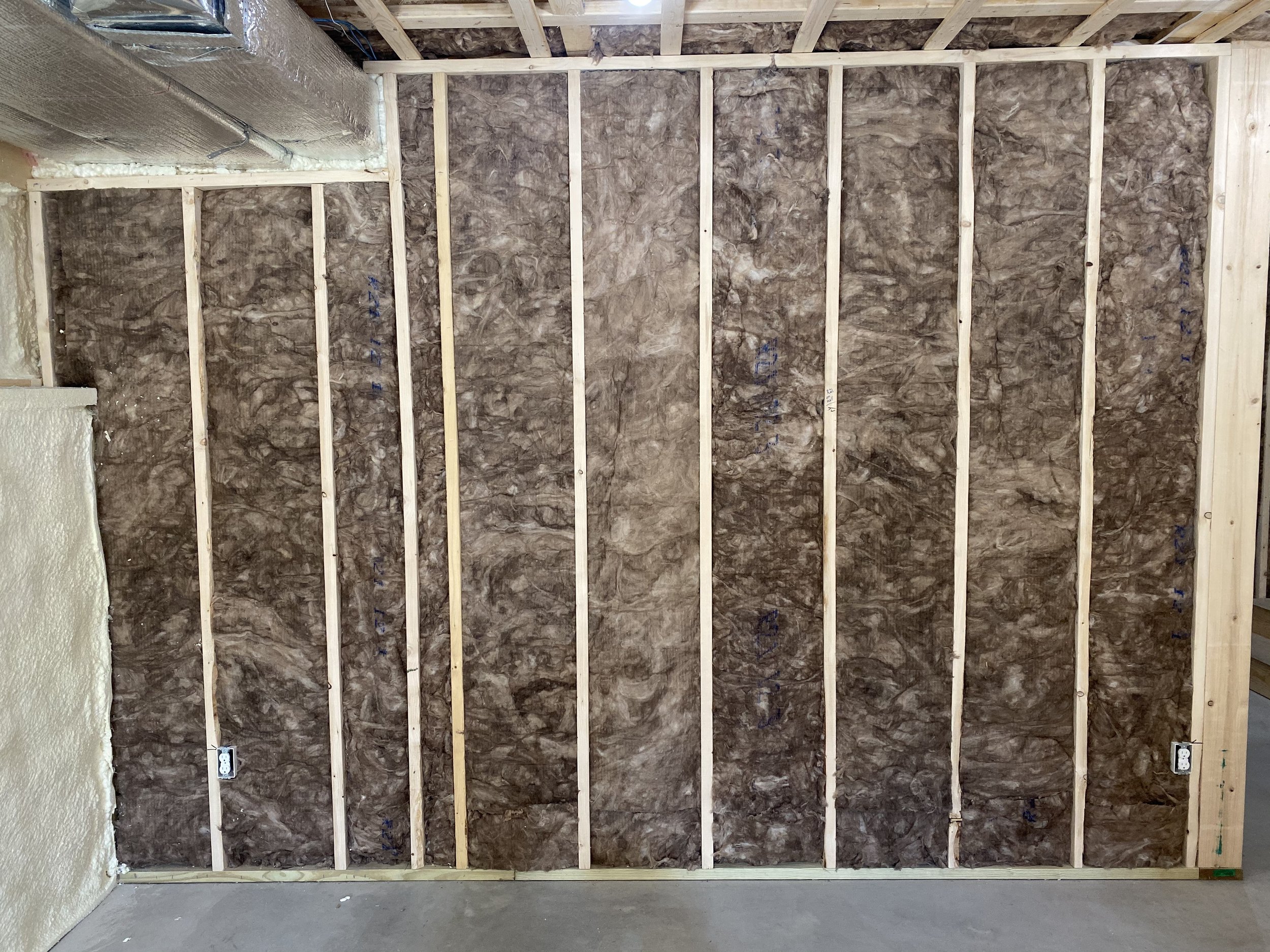
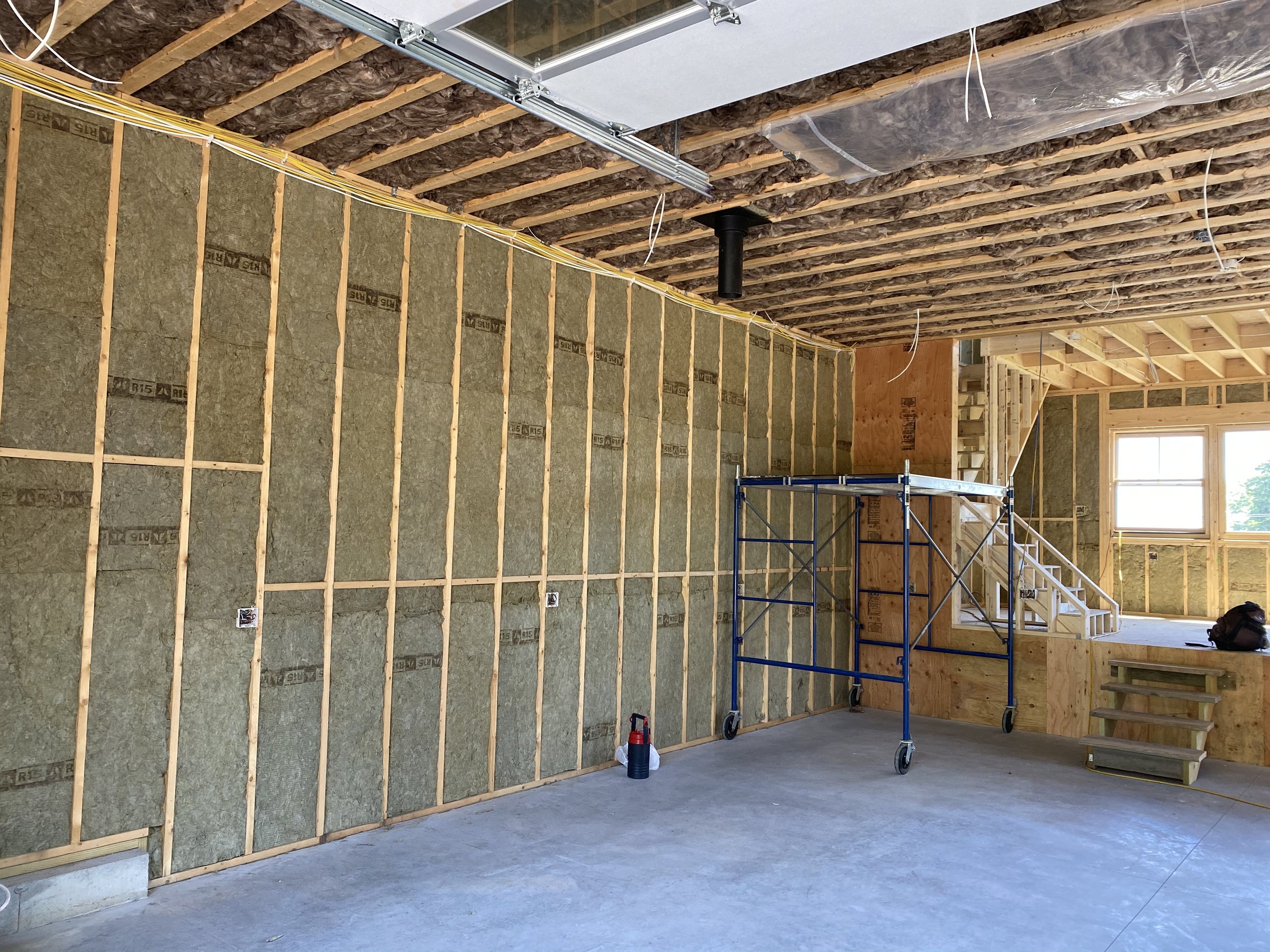